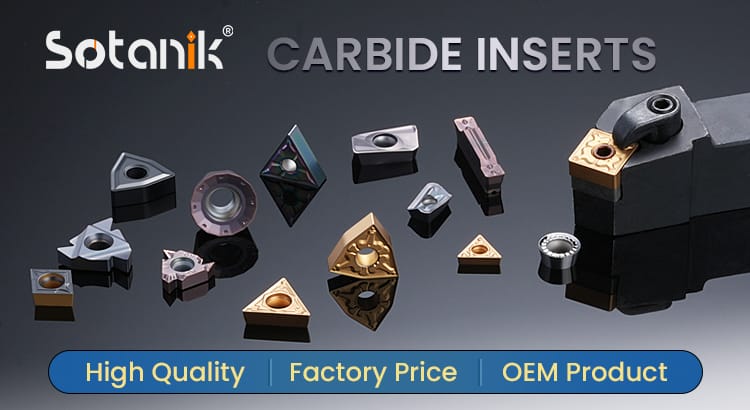
Mastering Carbide Insert Selection: A Systematic Approach for Machining Excellence
1. Material-Specific Grade Engineering
Workpiece composition dictates non-negotiable carbide grade parameters.
For ISO P-category steels, prioritize ultra-fine grain substrates (0.3–0.5μm) with medium-temperature PVD TiAlN coatings.
Stainless steels (M-group) require high-cobalt substrates (10–12% Co) enhanced by HIPIMS-applied AlCrN layers to combat work hardening.
Cast iron (K-class) performs optimally with medium-grain carbide and triple-layer CVD coatings (TiCN-Al₂O₃-TiN) to withstand abrasive particles.
Superalloys (S-group) demand TaC-reinforced substrates paired with nanocomposite AlTiSiN coatings.
Hardened steels >55 HRC necessitate mirror-polished cermet grades.
Always verify material hardness within ±3 HRC tolerances to prevent premature failure.
2. Cutting Geometry Optimization
Precision machining requires strategic geometric configuration. Finishing operations mandate sharp 35° diamond shapes (VNMG) with 7° positive rake angles and 0.02mm honed edges for minimal cutting forces. Heavy roughing necessitates negative-rake square inserts (SNMG) featuring T-land edge preparations (0.15mm × 25°) for impact resistance. Nose radius selection follows the 1.5x feed rule: Finishing (≤0.4mm feed) uses 0.2–0.4mm radii; roughing (≥0.3mm feed) requires 1.2–2.0mm radii. Threading applications demand full-profile inserts with polished flutes.
3. Chipbreaker Intelligence
Chip control geometry directly correlates with feed rates. For gummy materials (aluminum/stainless), select open geometries with nano-coatings to prevent built-up edges.
4. Cutting Parameter Boundaries
Establish velocity-feed guardrails based on coating technology. PVD AlTiN coatings support 380–420 m/min cutting speeds and 1.5x baseline feeds in dry conditions. CVD Al₂O₃ grades max at 350 m/min with flood coolant but resist abrasive wear. Diamond-coated inserts achieve 1,500+ m/min on non-ferrous alloys but fail catastrophically on ferrous materials. Violating Vc limits accelerates crater wear exponentially; insufficient feed induces depth-of-cut notching.
5. Failure Diagnosis & Countermeasures
Flank wear exceeding 0.3mm indicates coating inadequacy—upgrade to Al₂O₃ CVD or diamond coatings. Edge chipping signals insufficient substrate toughness—switch to ≥12% cobalt grades. Thermal cracks require high-pressure coolant (>70 bar) or reduced cutting speeds. Built-up edges necessitate polished surfaces or TiB₂ top layers. Document failure patterns using ISO 3685:1993 wear criteria.
 Â
6. Execution Roadmap
Certify workpiece material to ISO 4957 standards
Match geometry to operation forces
Select grade using supplier application maps
7. Calibrate equipment:
Verify <0.015mm runout
Align coolant jets within ±3° of cutting zone
8. Conduct test cuts:
Start at 70% recommended Vc;Â ramp 10% per pass until chips show uniform straw-yellow oxidation