FAQ
Professional supplier for cutting tools
SOTANIK TOOLS IS A INSERT CARBIDE MANUFACTURER
Our Carbide inserts include: Turning inserts, Milling inserts, Threading inserts, Grooving inserts and U drill inserts.
Today I will introduce our carbide turning insert,
There are many codes like: CNMG, DNMG, SNMG, TNMG, WNMG, VNMG, CCMT, DCMT and so on.
As example TNMG CNC turning insert,
TNMG160404-TM
TNMG160408-MAL
TNMG220404-SPM
TNMG220408-SPR
TNMG220408-ZEF
T is the shape
N represents the cutting edge clearance angle
M stands for tolerance
G stands for chip breaker and clamping style
16 or 22 is cutting length
The middle number 04 is thickness of insert
04/08/12 is the code for the radius.
TM/MA/SPM/ZEF is chip-breaker. According to different grade with different chip-breaker.
TNMG160404-TM HP1020 is for Soft steel. TM suits semi-finishing P material.
TNMG160408-MA HM2035 is for processing stainless steel, MA is suitable for semi-finishing M material
Of course we also have many grades. Now follow me to know more information.
HP1025 black coating is suitable for processing quenched and tempered steel below HRC25-35.
HP1050 two-color coating is suitable for HRC35-HRC45 hard steel for continuous processing.
HH6120 colorful coating is suitable for various difficult-to-machine materials, nickel alloys, chromium alloys
BN01 UN-coated suitable for aluminum
HK3115 black coating suitable for cast iron, intermittent machining.
Different grades usually with different chip-breaker too.
CARBIDE END MILL SERIES OF BWIN TOOL
BWIN TOOL manufactures a variety of carbide end mill series, including square end mill, ball end mill, corner radius end mill, thread end mill, roughing end mill, chamfer end mill, tapered end mill, dovetail milling cutter and so on, with different hardness HRC45, HRC55, HRC60 and HRC65.
Carbide end mills with different hardness grades are suitable for various processing needs. The following introduces their different processing materials.
HRC45 hardness milling cutter, suitable for processing mild steel, alloy steel, gray cast iron, ductile iron etc. It has good wear resistance and impact resistance, and it can maintain stable cutting performance during processing.
55 degree end milling cutter is a kind of milling cutter with medium hardness and strong versatility. If you want a milling cutter with strong versatility and good price, then the HRC55 milling cutter is very suitable for you. It can process carbon steel, alloy steel, stainless steel, aluminum, alloy, etc. It has excellent wear resistance and cutting performance.
HRC60 is a high hardness grade, suitable for hard materials such as super hard materials and various sticky materials. It has excellent cutting performance and wear resistance, and can maintain stable performance in complex processing environments.
HRC65 carbide end mill has the strongest versatility. In addition to processing carbon steel, harden steel, and stainless steel, it can also process extremely difficult materials such as super hard materials like hardened steel and super alloys. It has extremely high hardness and anti-wear properties, and it performs well under high speed machining and heavy load conditions.
CARBIDE INSERTS
The tungsten carbide inserts are divided into turning insert, milling insert, thread insert, grooving insert, and U drill insert. There are different chipbreakers depending on the processing requirements.
Finishing chipbreakers are:
-SPF, Unique design efficiently controls the form of chip and breaks chip; Sharp cutting edge, smooth cutting; Excellent surface quality.
-STF, Special chip breaker structure makes excellent chip breaking even at small cutting depth;Sharp cutting edge, cutting smoothly and quickly.
-SMF, Special designed rake angle and cutting edge inclination; Sharp cutting edge, small cutting force; Good machining surface quality
-MSF, Three-dimension designed with double rake angle; Sharp cutting edge and lower cutting resistance; Efficiently solved build up edge, work hardening and other machinging problems; Cutting edge inclination designation is good to control chip flow direction and obtains excellent surface quality.
Semi-Finishing chipbreakers are:
-SPM, Negative chamfer designation gives blade good strength; Double chipbreaker lands, make bigger chip control range.
-TM, Flat cutting edge design, good wear-resistance and breakage resistance; Inclination angle combination structure can control the chip breaking direction efficiently
-MAL, Special chipbreaker design to keep both sharp cutting edge and increased blade intensity; Efficiently solved break chip, high cutting temperature, sticking, work hardening and other maching problems; It has very excellent efficiency.
-General Chipbreaker, preferred groove type for cast iron turning.
Roughing chipbreakers are:
-SPR, Three-dimension designed with double rake angle, wide margin and nagative chamfer; Wonderful blade intensity gives a longer tool life time; Suitable for steel roughing machining.
-Flat, machining groove type in unstable working conditions of cast iron turning.
-TK chipbreakers, Finishing and Roughing, Specially designed for aluminum processing.
-M chipbreakers, Specially designed for Parting and Grooving.
CNC TUNGSTEN CARBIDE INSERT
CNC Tungsten Carbide Insert is mainly used for finishing and semi-finishing of materials such as Steel, Stainless Steel, Cast Iron, Aluminum, High-temperature Alloys, and Hard Steel. Include: Turning Insert, Milling Insert, U Drill Inserts, Thread Milling Inserts, and Grooving Inserts, etc, which are widely used in various fields.
In automobile manufacturing, CNC Tungsten Carbide Insert is used to cut and process automobile parts, such as engine parts, body panels, Automobile chassis etc. In the aerospace field, the Insert are used to process aircraft and rocket parts, such as wing surfaces and fuselages.
In addition to the manufacturing industry, CNC Tungsten Carbide Insert also plays an important role in the construction industry. In construction, it used to cut materials such as Concrete, Stone, and Steel. Their sharpness and durability enable them to efficiently complete various cutting tasks and improve construction efficiency.
CNC Tungsten Carbide Insert is also widely used in agriculture and gardening. Farmers and gardeners use Carbide Inserts to prune trees, mow grass, and harvest crops.
In conclusion, Carbide Inserts are a versatile tool that is widely used in manufacturing, construction, agriculture, gardening, etc. Their precision cutting ability and durability make them one of the indispensable tools in all walks of life.
CLASSIFICATION OF MILLING CUTTERS

Carbide end mills are a type of tool used for milling with one or more flutes.They can be classified in many ways:
Based on Cutting Edge Shape: Carbide Square End Mill, Carbide Ball Nose End Mill, Corner Radius End Mill, Roughing End Mill, Thread End Mill Cutters, 45 Degree Chamfer End Mill, Taper Ball End Mill, Micro diameter end mill, etc.
Based on Material Compatibility: it have Carbide End Mill For Steel (with Coating): Typically coated with materials like AlTiN, TiSiN, AlTiSiN, or other advanced coatings to enhance performance when hardened steel. And Carbide End Mill For Aluminum (without coating or DLC Coating): Often without coating or coated with Diamond-Like Carbon (DLC) to prevent galling and improve lubricity when cutting aluminum.
Based on Hardness Rating and Coating: HRC45 Solid Carbide End Mills (AlTiN Coating), HRC55 Carbide End Mills (TiSiN Coating), HRC60 End Mill (Nano black Coating), Carbide End Mill HRC65 (Nano Blue Coating)
Milling cutters are suitable for cutting various materials. They can be used for cutting metals, such as aluminum alloys, copper, steel, etc., and can also be used for cutting wood and plastics, such as furniture, floors, plastic pipes, plastic boards, etc. They are very common machining tools in factories.
BWIN END MILL: THE BEST CHOICE FOR PRECISION MILLING
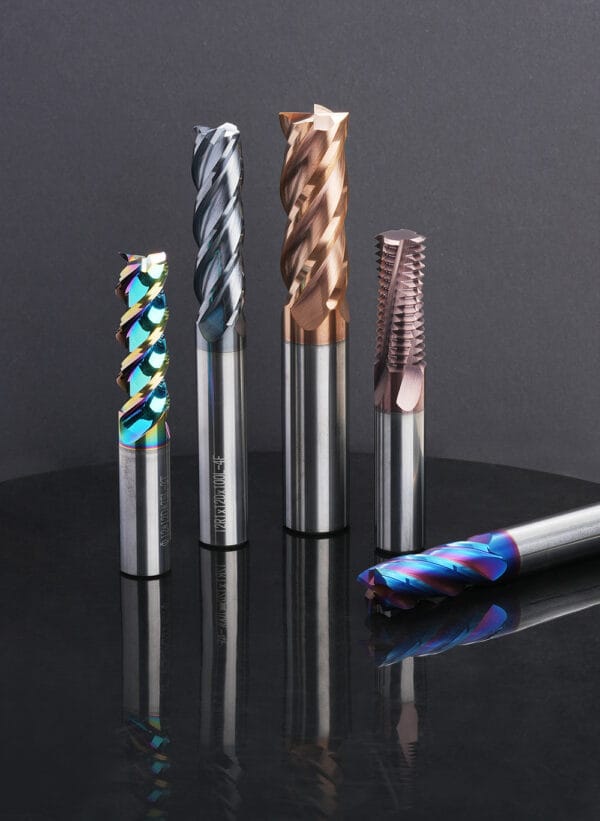
End mills are one of BWIN’s main products and are very popular with customers. These end mills meet the needs of processing different materials with their excellent hardness adaptability and diverse helix angle designs. Here are some key features of BWIN end mills:
1. BWIN sells various types of End mills
At present, the end mills we sell most are flat end mills, ball nose end mills, and corner radius end mills.At the same time, in order to enrich our product categories and to meet the different needs of customers, we also produce thread end mills,roughing end mills, chamfer end mills,T-Slot end mills, Inner-R end mills, arch end mills and so on.
All regular sizes are in stock, and we can also provide customized services according to the different needs of customers.
2. End mills of different hardness and their applications
BWIN end mills can process materials of different hardness according to different hardness grades:
HRC45(AITiN-black coated): It’s suitable for machining ordinary carbon steel, cast iron or alloy steel with lower hardness. This type of end mill is usually used for rough machining and semi-finishing of medium hardness materials, which can ensure good cutting effect and quality.
HRC55(TiSIN- bronze coated): It’s suitable for machining steel, compared with HRC45, HRC55 can be used for harder materials, providing better wear resistance and longer cutting life time.
HRC60(AlTiSiN- Nano black coated): It’s suitable for difficult-to-machine steel parts, stainless steel and heat-resistant alloys. It has excellent cutting performance and wear resistance, and can maintain stable performance in complex processing environments.
HRC65(AlTiSiN- Nano blue coated): It’s suitable for extremely difficult materials such as hardened steel. It has extremely high hardness and anti-wear properties, and it performs well under high-speed machining and heavy load conditions.
3. Use of different helix angles
The helix angle of BWIN flat end mills is 35°, that of aluminum flat end mills is 45°, and that of ball nose end mills and corner radius end mills is 30°. These helix angles facilitate better chip evacuation, thus increasing productivity.
At the same time, we also provide tool holders and collets for use with end mills. If you are interested, please feel free to contact us for more information.
BWIN THREAD END MILL

BWIN offers a wide variety of end mills. In addition to conventional end mills, thread end mills are also very popular. BWIN thread end mills meet various machining needs with their excellent performance and diverse designs. The following is an introduction to the features of BWIN single-tooth, three-teeth, and full-teeth thread end mills.
Single-tooth thread end mills are known for their unique single-tooth design. This design reduces the contact area between the tool and the workpiece, thereby reducing cutting forces. Single-tooth end mills are particularly suitable for processing deeper threads because they can effectively avoid tool deflection and improve thread processing accuracy.
BWIN brand three-teeth thread end mill is famous for its high precision and high efficiency. This end mill is made of carbide material, which has excellent wear resistance and strength. The three-teeth design enables the end mill to achieve more stable cutting, reduce vibration and improve processing accuracy during processing. In addition, the three-teeth thread end mill is suitable for a variety of materials and pitches, and has high versatility.
Full-teeth end mill are known for their complete thread processing capabilities. The design of this end mill allows it to complete the entire thread processing in one operation without layering, so the processing efficiency is high. This end mill is suitable for applications that require fast and accurate processing of complete threads.
BWIN provides you with a wealth of choices. You can better choose the tool suitable for your processing task by understanding the characteristics of these different types of thread end mills according to your processing needs, material properties and precision requirements.
BWIN TURNING TOOL HOLDER
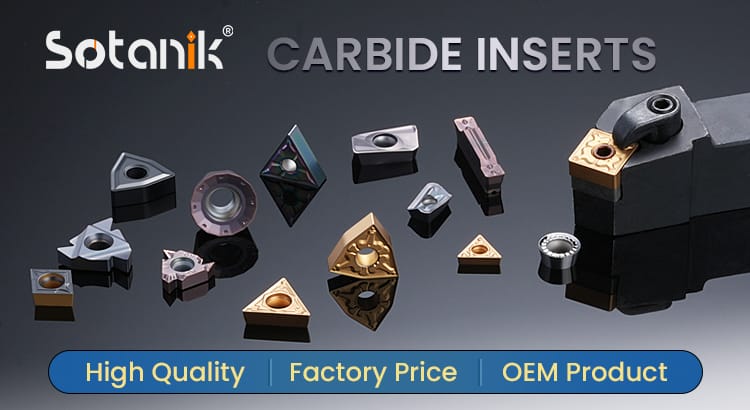
Turning Tools are usually made of tool steel and can be divided into Cylindrical Turning Tools and Internal Turning Tools. Common fastening modes include D-type, M-type, W-type, S-type, P-type, etc.
In the model of Turning Tool, each letter/number has its own meaning.
For example, in Cylindrical Turning Tool MCLNR2525M12,
“M”: Fastening mode is M-type,
“C”: Shape of blade is a quadrilateral,
“L”: Cut-in angle is 95°,
“N”: Blade gap angle is 0°,
“R”: Blade direction,
“25”: Height,
“25”: Width,
“M”: Length,
“12”: Cutting edge length.
S25R-MCLNR12 is Internal Turning Tool,
“S”: material is alloy steel,
“25”: the diameter of the handle is 25,
“R”: length is 200,
“M”: clamping method is M type,
“C”: blade shape is quadrilateral,
“L”: cutting angle is 95°,
“N”: blade gap angle is 0°,
“R”: blade direction,
“12”: cutting edge length.
Turning Tool is used to install Turning Inserts, such as CNMG, DNMG, SNMG, TNMG, WNMG, VNMG, CCMT, DCMT, SCMT, TCMT, WCMT, VBMT, VCMT, RCMT, etc.
For example:
Cylindrical Turning Tool MCLNR2525M12 can be installed with CNMG1204 turning inserts,
MDPNN2525M15 can be installed with DNMG1504 and DNMG1506 tungsten carbide insert knives.
Internal turning tool “S25S-MTFNR16” can be installed with TNMG160408 tungsten carbide inserts,
S32T-MVQNR16 can be installed with VNMG1604 tungsten carbide inserts CNC.
SOTANIK CARBIDE INSERTS 01
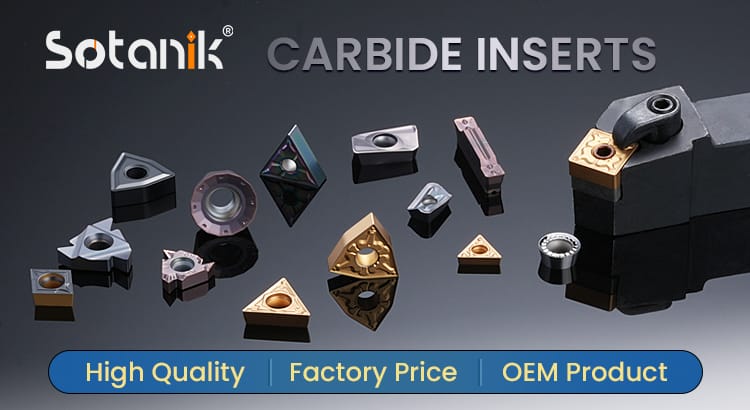
Shenzhen BWIN Precision Tools Co., Ltd. mainly deals in carbide inserts. Today we mainly introduce threading inserts, grooving inserts and milling inserts.
There are many kinds of threading inserts, including universal thread 60, standard thread ISO, American thread UN, American standard taper pipe thread NPT, British Whitworth thread for BSW BSP, American 29° trapezoidal thread ACME, etc. We sell them all, and the most popular one is the universal thread.
Grooving inserts are mainly used for external circle grooving, internal hole grooving, end face grooving, etc. We are currently mainly selling MGMN double-head and SP single-head grooving carbide inserts.
Milling inserts are mainly used for milling tool: face milling cutter and milling bar.
Milling inserts we sell mostly is APMT inserts, but we can provide other milling inserts: RPMT, RDMT, RPMW and so on.
We provide different grades of threading inserts, milling inserts and grooving inserts for processing different materials.
HT2015 is suitable for processing steel, stainless steel, and cast iron.
HM2035 is suitable for processing stainless steel,
BM085 is suitable for high-hardness materials such as nickel alloys.
HP1020 is suitable for processing steel parts.
BN01 is suitable for processing aluminum.
HK3115 is for cast iron.
Our carbide inserts are of good quality and low price, and are well received by customers. Many customers place orders repeatedly and have long-term cooperation.
According to the real feedback from customers of different markets, our carbide inserts are comparable to some well-known brands.
SOTANIK CARBIDE INSERTS 02




Shenzhen BWIN Precision Tools Co., Ltd is a professional carbide inserts manufacturer. Earlier I introduced the types of our blades and the grades of coatings.
Today I will introduce the chip-breaker of inserts.
For steel process, we some some grooving type like TM, PM, it is for semi-finishing process.
For stainless steel, MAL, MSL, HS, MF grooving type is suitable for semi-finishing process.
For cast iron, it is usually general chip-breaker for semi-finishing cutting.
For roughing process, we have ZM, SPR for P material.
Instead for M material, GS is a kind of grooving type choice for roughing.
While flat chip-breaker for cast iron roughing cutting.
If customer want to finishing process, we have many chip-breakers, usually we sell these: MQ, SF, HA, CQ, JHQ, FML, MSF.
We also have some new chip-breaker now.
JHQ/JGQ/SPF Chip Breaker: Suitable for finishing lSO P material.
FML/MSF/STF Chip Breaker: Suitable for finishing ISO P and M material.
As we all known, the life-time of inserts depends not only on the correct material and processing method, but also on the appropriate processing speed and parameter.
Our carbide inserts are popular in various markets around the world and have been used by many customers to replace many well-known brands. The groove type and grade of our blades are no less than other well-known brands.
BWIN CARBIDE ROTARY BURRS


BWIN manufactures a wide variety of CNC tools, and carbide rotary burrs are one of our main products. Carbide rotary burrs are a common hand tool, mainly used for finishing and shaping in metal processing. It is made of solid metal material and has sharp file teeth, which can effectively smooth out the uneven surface of the workpieces, thereby improving the quality and appearance of the workpiece.
BWIN brand provides a variety of shapes of carbide rotary burrs to suit different processing scenarios:
A type(Cylindrical): Suitable for machining workpieces surface contours.
B type(Cylindrical with end teeth): Suitable for machining workpieces surface contours and right-angle intersections.
C type(Ball nose cylindrical): Suitable for machining arc contours.
D type(spherical): Suitable for machining arc contours of workpieces and removing burrs on diameters and welding points.
E type(Oval): Suitable for machining arc contours of workpieces.
F type(Ball nose tree type): Suitable for processing arc contours in confined spaces.
G type(Pointed tree shape): Suitable for machining arc contours and sharp corners with limited spaces.
H type(Flame shape): Suitable for processing complex surfaces, grooves and fine finishing of narrow areas.
J type(60° Countersink): Maching of acute-angled areas, countersinking beveling/chamfering at defined angles.
K type(90° Countersink): Maching of acute-angled areas, countersinking beveling/chamfering at defined angles.
L type(Tapered with round end): Suitable for machining bevels, chamfers and transition areas of complex surfaces.
M type(Cone shape): Work on narrow contours and surfaces, surface maching.
N type(Invered cone): Edge maching from the rear in hard to reach areas.
These are the types we sell most often. We have a wide variety of sizes, including 4mm, 6mm, 8mm, 10mm, 12mm, 14mm, and 16mm blade diameters for you to choose from. We also offer single-edge and double-edge options. For more details, please look them up in our catalog.
The product advantages of the BWIN brand are not only reflected in its excellent performance, but also include simple and convenient use, safety and reliability, and significantly reduced overall processing costs. These advantages make the BWIN brand an indispensable partner in the manufacturing industry. We welcome you to test our products.
BWIN HRC45 CARBIDE END MILL

Carbide end mill has many different materials. According to different needs, customers can choose HRC45, HRC55, HRC60, HRC65.
HRC45 Carbide end mill is popular with customers for its economical price.
Main applications: shoulder milling, side milling, face milling, slot milling.
HRC45 coating is AlTiN black coating
Hardness (HV) :3300
Thickness (UM):2.5-3
Oxidation Temp.(℃):900
Friction Coeffient:0.3
suitable for rough grooving and semi-finishing of steel, cast iron. Standard sizes from 1mm-20mm are in stock, and customized sizes are also acceptable.
Cutting diameter tolerance -0.01/-0.03mm (D1-D4); -0.01/-0.04mm (D6-D20). Shank diameter tolerance H6 (0/-0.01)mm.
HRC45 flat end mill has 2F and 4F, the standard helix angle is 35°. Ball nose end mill, the standard helix angle is 30°, the arc back angle makes the tool more wear-resistant, and the flat back angle makes the tool sharper and stronger, the cutting process is lighter and faster, and the tool life is longer under the double cooperation, and the appropriate one can be selected according to different processing conditions.
If other customized milling cutters are needed, we can also customize production according to drawings to meet customers’ needs.
APPLICATION OF CARBIDE INSERT
With the rapid development of science and technology, carbide insert technology has gradually shown widely used application in many fields with its unique advantages. As an important part of modern industrial manufacturing, carbide insert technology has brought revolutionary changes to all walks of life with its accurate and efficient characteristics.
In the field of automobile manufacturing, carbide insert technology plays an important role. Whether it is engine parts, transmission systems, or brake systems and suspension systems, carbide insert technology can produce high-quality automotive parts with its precise processing capabilities. These parts not only have higher precision and life, but also effectively improve the performance and quality of the car, bringing consumers a safer and more comfortable driving experience.
In the field of aerospace manufacturing, the application of carbide insert technology is even more indispensable. Aerospace parts have extremely high requirements for processing accuracy and quality, and carbide insert technology can just meet these stringent standards. Whether it is engine parts, wing parts, or metal structures for aviation, carbide insert technology can provide high-quality parts for the aerospace manufacturing industry with its excellent processing capabilities, thereby ensuring the performance and safety of aircraft.
In addition, in the field of electronic manufacturing, carbide insert technology also plays an important role. Electronic parts have extremely high requirements for processing accuracy and surface finish, and carbide insert technology can just meet these requirements. From semiconductor chips, circuit boards to electronic components, carbide insert technology can provide high-quality products for the electronic manufacturing industry with its fine processing capabilities, and promote the continuous development and progress of electronic technology.
CARBIDE ROUGHING END MILL

Carbide roughing end mil, A rotating tool with one or more teeth used for rough milling.
1. According to the coating, there are mainly AlTiN coating, TiAlN coating and non-coating.
HRC45 Roughing end mill is mainly AlTiN coating, suitable for processing carbon steel, alloy steel, cast iron, general iron, etc.
HRC55 Roughing end mill is mainly TiSiN coating, suitable for processing stainless steel, mold steel, tool steel, general iron, etc.
Non-coating mainly processes Non-ferrous metal materials,aluminum, copper, etc.
2. According to the length, there are general length and extended length. Conventional size 1-20mm: 50-150mm long
Features:
1. Suitable for rough processing.
2. High processing efficiency.
3. Good chip removal performance and large chip removal volume.
4. Has a high metal cutting rate.
It also has certain shortcomings when in use: first, its chip groove is small, and the chips are not easy to discharge; second, because the chip groove is small and narrow, it is easy to break the edge when processing some workpieces with complex shapes.
Application:
Mostly used for slot processing, woodworking milling cutter, step surface processing.
If need special size or processing material, we can also support customization.
BWIN THREADING TOOL
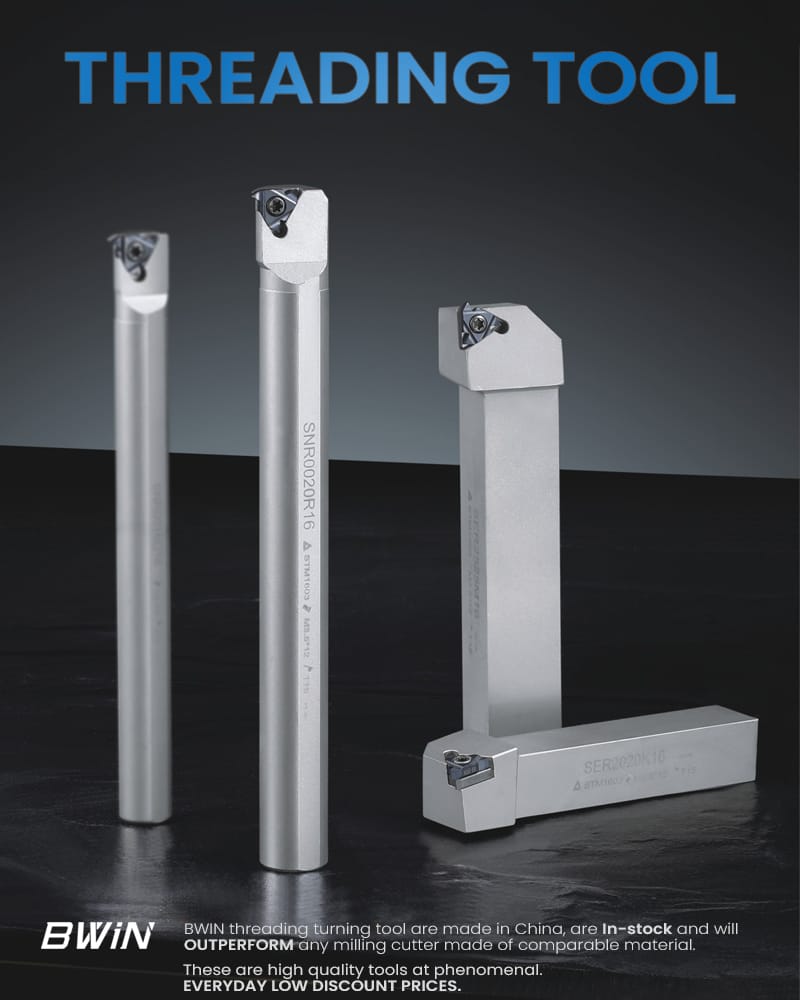
Threading tool is a commonly used machining tool, which is used to machine threads on workpieces after installing threaded inserts. It can be divided into external threading tool holders and internal threading tool holders. Generally speaking, the shape of tungsten cemented carbide inserts should match the shape of the thread, and the size of tungsten carbide inserts should be slightly smaller than the size of the thread to ensure that the tungsten carbide insert knives can smoothly enter the threaded hole.
In machining, in order to ensure the quality and efficiency of thread processing, when selecting threading tool and carbide threading inserts, it is necessary to ensure that their sizes and specifications match. When equipping carbide threaded inserts, multiple factors need to be considered, such as the size and model of the threading tool.
For example:
The threading tool SEL1212H11, whose tool holder size is 12*12mm, can be equipped with a carbide threading insert of 11ELXX.
The threading tool SEL2525M22, whose tool holder size is 25*25mm, can be equipped with a carbide threading insert of 22ELXX, and it is a left-hand tool.
There are also products such as Threading tool SER2020k16, whose tool bar size is 20*20mm, and can be equipped with carbide threading inserts of 16ERXX, and it is a right-hand tool.
In addition, the thread turning tool bar SNR/L0013M11 can be equipped with carbide inserts of 11NR/L–.
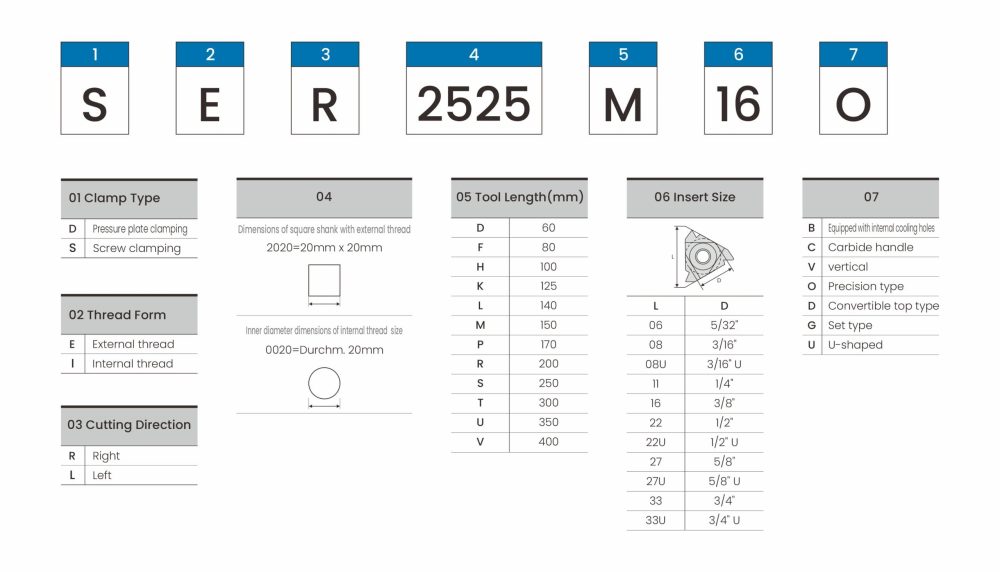
SOTANIK U-DRILL INSERT
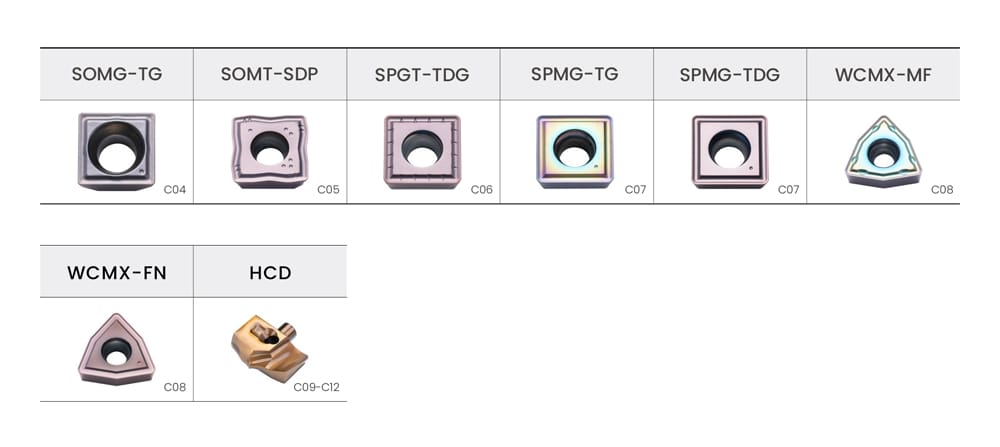
SWISS-TYPE LATHE CUTTING INSERT
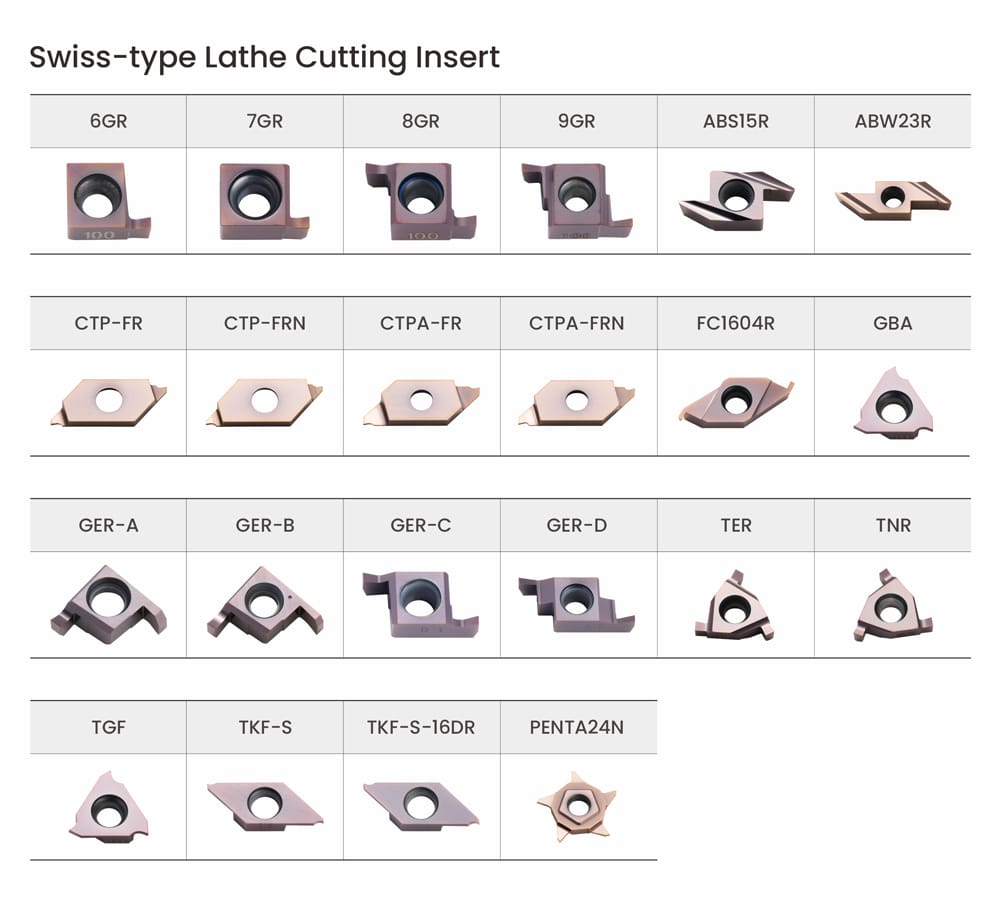